A rotating road wheel allows the driver to maintain steering control under heavy braking by preventing a skid and allowing the wheel to continue interacting tractively with the road surface as directed by driver steering inputs. ABS offers improved vehicle control and decreases stopping distances on dry and especially slippery surfaces. However, on loose surfaces like gravel and snow-on-pavement, it can slightly increase braking distance while still improving vehicle control.[1] On others, it may not improve control at all.
Since initial widespread use in production cars, anti-lock braking systems have evolved considerably. Recent versions not only prevent wheel lock under braking, but also electronically control the front-to-rear brake bias. This function, depending on its specific capabilities and implementation, is known as electronic brakeforce distribution (EBD), traction control system, emergency brake assist, or electronic stability control.
Early Anti-lock Brake System
Anti-lock braking systems were first developed for aircraft use in 1929, by the French automobile and aircraft pioneer, Gabriel Voisin, asthreshold braking on airplanes is nearly impossible. An early system was Dunlop's Maxaret system, introduced in the 1950s and still in use on some aircraft models.[2] These systems used a flywheel and valve attached to the hydraulic line that fed the brake cylinders. The flywheel was attached to a drum that ran at the same speed as the wheel. In normal braking the drum and flywheel would spin at the same speed. If the wheel slowed suddenly the drum would do the same, leaving the flywheel spinning at a faster rate. This caused the valve to open, allowing a small amount of brake fluid to bypass the master cylinder into a local reservoir, lowering the pressure on the cylinder and releasing the brakes. The use of the drum and flywheel meant the valve only opened when the wheel was turning. In testing, a 30% improvement in braking performance was noted, because the pilots immediately applied full brakes instead of slowly increasing pressure in order to find the skid point. An additional benefit was the elimination of burned or burst tires.[3]In 1958 a Royal Enfield Super Meteor motorcycle was used by the Road Research Laboratory to test the Maxaret anti-lock brake.[4] The experiments demonstrated that anti-lock brakes could be of great value on motorcycles, where skidding is involved in a high proportion of accidents. Stopping distances were reduced in almost all the tests compared with locked wheel braking, but particularly on slippery surfaces, where the improvement could be as much as 30 percent. Enfield's technical director at the time, Tony Wilson-Jones, saw little future in the system, however, and it was not put into production by the company.[4]
A fully mechanical system saw limited automobile use in the 1960s in the Ferguson P99 racing car, the Jensen FF and the experimental all wheel drive Ford Zodiac, but saw no further use; the system proved expensive and, in automobile use, somewhat unreliable.
Modern Anti-lock Brake System
Chrysler, together with the Bendix Corporation, introduced a true computerized three-channel, four sensor all-wheel antilock brake system called "Sure Brake" on the 1971 Imperial.[5] It was available for several years thereafter, functioned as intended, and proved reliable. General Motors introduced the "Trackmaster" rear-wheel (only) ABS as an option on their Rear-wheel drive Cadillac models in 1971.[6][7] In 1971Nissan offered EAL(Electro Anti-lock System) as an option on the Nissan President, this became Japan's first electronic ABS(Anti-lock braking system).[8]In 1975, Robert Bosch took over a European company called Teldix (contraction of Telefunken and Bendix) and all patents registered by this joint-venture and used this acquisition to build the base of the ABS system introduced on the market some years later. The German firmsBosch and Daimler-Benz had been co-developing anti-lock braking technology since the early 1970s, and introduced the first completely electronic 4-wheel multi-channel ABS system in trucks and the Mercedes-Benz S-Class in 1978.[citation needed]
The modern ABS system applies individual brake pressure to all four wheels through a control system of hub mounted sensors and a dedicated micro-controller. ABS is offered, or comes standard, on most road vehicles produced today and is the foundation for ESC systems, which are also rapidly increasing in popularity due to the vast reduction in price of vehicle electronics over the years.









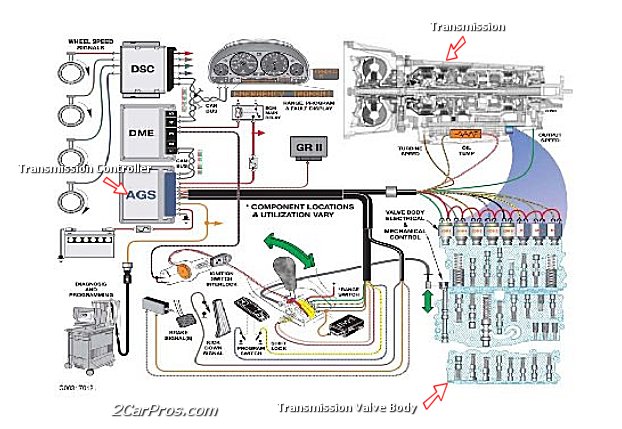
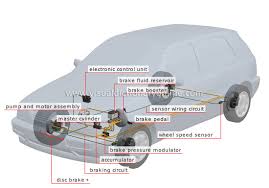


Anti-lock brake systems are designed to minimize and control wheel lock up during braking. Wheel lock, also known as wheel slippage, can have a dramatic affect on the control of the vehicle during braking. Wheels that are locked up, with the tires sliding across the road surface, cannot be controlled by the vehicle operator. The driver is just along for the ride until wheel slippage is reduced to a point where vehicle control is regained. Braking performance is also affected by wheel slippage. The effectiveness of the automotive braking system depends on the ability of the tires to grip the road surface. When the wheels are locked up during braking, the friction for braking is generated by the tires sliding on the pavement, not between the brake pads and the rotor surface. The heat generated during such an event is dissipated very poorly by the tires. The brake linings and the rotor or drum surfaces are much better suited to dissipate the heat generated by friction. Rolling tires with good road surface adhesion when coupled with an efficient brake system, will provide the best stopping performance for a vehicle. The ABS system is able to monitor the slippage of the individual wheels during stops and control the braking of any or all wheels that may lock up. The control module determines wheel slippage by monitoring wheel speed sensor information while braking. A wheel that is exhibiting noticeably slower speeds than the other wheels, would be considered locked up and be selected for brake lock up control. Wheel lock up control is accomplished by modulation of the brake pressure, to the affected wheel or wheels.
ABS CONTROL MODULE
The ABS control module is a microprocessor that is used to manage the operation of the ABS system. The ABS control module monitors and processes information from various sensors, modulates pressure to the brake system and carries out self-diagnostic tasks. Some of the inputs to the ABS module are the wheel speed sensors, brake switch, brake warning light, parking brake switch, pressure modulation devices and ignition and power feeds. The output controls consist of brake pressure modulation components and the anti-lock brake lamp. Most ABS control modules have the ability to run self diagnostic tasks and store trouble codes for failed diagnostics. The ABS control module can display this information to a scan tool or through flash codes, via the dash mounted anti-lock brake light, making troubleshooting and repair more accessible. Some ABS control modules store sensor information when a failed diagnostic is recorded. This can assist automotive technicians in diagnosing ABS trouble codes by displaying a record of sensor information at the time of the failed diagnostic.
WHEEL SPEED SENSORS
Wheel speed sensors are used by the ABS control module to monitor wheel lock up. Wheel speed sensors consist of a toothed wheel, mounted on the wheel hub or axle shaft, so as to rotate when the wheel is in motion. A magnetic sensor is placed at a fixed location, a calibrated distance from the toothed wheel. The air gap between the toothed wheel and the magnetic sensor is usually around .040 to .060 in (refer to your auto repair book for the exact spec). When the tooth wheel rotates past the magnet on the sensor, an AC voltage is produced. The AC voltage output of the wheel speed sensor increases as the wheel speed increases. The ABS control module monitors this voltage to calculate wheel speed for ABS operation. If the ABS control module senses lower voltage from one sensor during braking, it will translate that as slower speed at that wheel and modulate brake pressure to control brake lock up.
HYDRAULIC MODULATOR
Brake lock up control is accomplished by rapidly applying and releasing the brakes of the affected wheel. To achieve this, the ABS control module is able to modulate brake hydraulic pressure to individual wheels. Brake pressure modulation is attained through several different methods. Design of the pressure modulation system varies according to vehicle design. One type of brake pressure modulator system uses solenoid operated valves to control brake pressure to individual wheels. The solenoids and valve arrangements are able to increase, hold or release brake hydraulic pressure to the brake system of a wheel. This system incorporates a hydraulic fluid pump to return fluid to the master cylinder and an accumulator to store excess brake fluid. When ABS operation is demanded, the control module operates the solenoid valves to hold or release pressure to one or all of the wheels, to control wheel lock up. A more recent design (and simpler to troubleshoot) uses high speed electric motors to seat and unseat hydraulic valves to control brake pressure during ABS stops. The electric motors are able to cycle the pressure modulation valves many times per second, to control wheel lock up. This design is less expensive to produce, since it does not require a hydraulic pump and accumulator as opposed to earlier designs.
ABS WARNING LIGHT
The ABS warning light operation is managed by the ABS control module. It is located in or near the instrument cluster and is used to warn the vehicle operator of a malfunction in the ABS system. In the event of a failure in the ABS system, the ABS warning lamp is illuminated to warn the driver. Some systems will inhibit ABS operation when the ABS lamp is illuminated. Refer to a manufacturer's manual covering your particular year/make/model automobile for the diagnostic and troubleshooting details before embarking on an auto repair project involving the ABS system.


No comments:
Post a Comment